RED METAL MINING
The Power Behind the Mine
Supplying specially made, high-quality, super strong transformers and electrical equipment for use deep in African mines, Red Metal Mining Project Engineers have seen it all. A long history in the mining industry combined with an innovative and problem-solving nature makes for a business that is the perfect partner for new mines, expansions, or extensions. CEO Lionel Wagner tells Enterprise Africa more about keeping mines electrified.
The world’s mines use a monumental amount of electricity to unearth the valuable minerals that we need to live and work. Powering progress is difficult and costly. Typically in remote, rural locations, bringing reliable electricity supply to mines is an engineering challenge. And when the power arrives on site, working with it to remain safe and usable is a fresh hurdle for local teams to jump. In South Africa, where electricity supply is a major national problem, the mines are coming up with new solutions to keep the lights on.
Whatever the source – whether Eskom grid, solar installation, furnace generation, or any alternative – when the power is generated, it must then be transported underground and made usable. Doing so in a safe and sustainable way is a major problem. Usually coming in at 11,000 volts, the current is dropped to allow for safe working with machinery and tools. Specialists head to the face in the mining shaft, often deep underground, and drill shotholes, where explosives blast away rock to be transported up and away for processing.
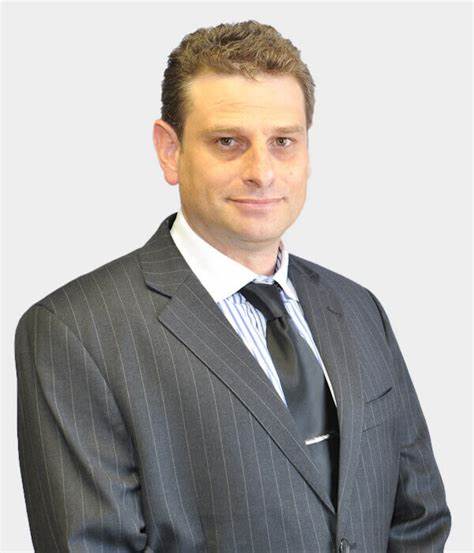
For this, specialist transformers are required. Robust, durable, temperature controlled, built to size, and above all, safe, these are essential high-performance assets that must be supplied by experts.
Edenvale-based Red Metal Mining Project Engineers (RMM) is an industry leader in the design, manufacture, maintenance, and support of transformers for the mining industry, allowing miners to work at optimal levels, without interruption resulting from electrical failure or voltage drops.
It’s highly technical, highly skilled work, and CEO Lionel Wagner tells Enterprise Africa that building a reputation for quality is the only way to be sustainable.
“The big mines want units that won’t fail. The engineers come to our facility and see the quality of our work, they inspect our processes. They meet our people and hear about our reputation. We get a lot of business this way, and we have a strong pipeline going forward.”
RMM is the sole agent for SGB in sub-Saharan Africa for cast resin dry-type transformers. SGB is the world’s leading manufacturer, based in Germany. Combined with RMM’s local expertise, the end result is a transformer that boasts superior quality and safety.
Transformers arrive at the company’s 3000 m2 site in Gauteng before being craned into the manufacturing space and being housed in the RMM custom-designed unit. From here, through a set of ISO certified processes, the company creates 1000kVA to 25 mVA cast resin dry-type transformers and underground cast resin mini substations, as well as oil immersed transformers.
“We handle consulting for companies that need to upgrade their mines. We have electrical engineers, mechanical engineers, and next year we will have the South African Bureau of Standards (SABS) quality mark,” says Wagner.
The success of the brand and its reputation for quality product and service has taken RMM beyond South Africa’s borders, opening an office in Zambia, to assist the country’s crucial copper industry, and also supporting projects in Angola, Zimbabwe, and Congo. Interest from India and Ethiopia and other parts of the world reinforces the idea that RMM is doing the right thing.
Wagner highlights the strength of the company with a 2016 disaster after which the product is still working as normal today.
“We supplied a transformer that got hit by lightning seven years ago. The housing crumbled and they sent it back to us for repair. We took off the housing and we cleaned it up. There was a small copper buzz bar that blew the terminal off. We replaced it and it was back to 100% – after a full lightning strike. The client was very happy, and we have since sold them another 150 transformers.”
SOLE SUPPLIER
RMM was established in 2006, supplying oil transformers into Zambia. When the focus changed to cast resin dry-type transformers, with miners preferring to not have oil underground, the company was careful with innovation and became one of the only businesses to understand the unique needs of African mines.
“Everybody rushed to market and came back with these big products that couldn’t fit down the shaft,” says Wagner. “I flew to Germany and got the sole rights as the sub-Saharan Africa distributor for cast resin transformers. We came up with a design and cooling pack to cool the transformer that fits into the winder cage.”
An electrical and mechanical engineer, with decades of experience in the mining industry, Wagner is a seasoned entrepreneur who enjoys the practical work.
“I like to be there. I can’t sit still,” he says. “I did my apprenticeship as an armature winder and I started my first business aged 21, repairing electric motors. I then became a workshop manager and design engineer for another company. I learned about designing electric motors and mechanical engineering, and I learned about SolidWorks drawing and flow simulation. I have met many engineers who are purely theoretical and know nothing about doing the work on the ground.”
Growing the business has seen Wagner build a team from just a few engineers in a small office, becoming a multi-factory, multi-national manufacturing company with 25 experts able to travel around the continent to keep mining moving deeper and further.
“We sell mini subs all over Africa and we just picked up a nice order in Congo. We recently sold 75 subs to a big, diversified miner and 100 to a big coal miner. Our target is to reach R250 million next year,” he says.
“We sell a lot of 630 kVA mini subs,” he adds. “There is always a demand for these products.” As miners move along a horizontal underground shaft, they must put a new mini sub every 800m to avoid voltage drops and keep drills and generators powered.
‘THEY NEED POWER’
In South Africa, RMM remains busy across all types of mine – coal, gold, iron, zinc etc. Every mine requires transformers and the company has become a preferred supplier for many of the international mining houses with multiple sites in SA. In Zambia, copper mining continues to boom as demand for modern battery minerals grows quickly. Congo has some of the world’s largest cobalt reserves – a key mineral in the production of batteries for electrifying society.
“To mine, they need power, and for power, they must have transformers to take high voltage of 11,000 on overhead lines down to 6.6 and eventually 5.3 volts,” explains Wagner.
“We manufacture PV transformers but once the transformer is there on the mine, it doesn’t matter about the energy source, the transformer is the same.”
Mines have been aggressive about ensuring their power supply and many are turning to renewable energy projects – solar or wind – to energise their sites when national grid supplies become unreliable. For RMM this does not impact workflow or quality. The company is experienced in transformer connections for all types of supply and is excited that the mines continue to show ambition and innovation.
“The mines are taking things into their own hands. They are putting up their own power plants and they are not waiting for others to dictate the future. One of the big companies just put up a new power plant that cost R30 billion – they are not standing still, they know they need power, and they know they must spend money,” says Wagner.
This is why RMM has invested heavily in the oil transformer side of the business – to give clients across different regions and projects a choice. Today, engineers can pick cast resin or oil transformers, cast resin or oil substations, furnace oil transformers, oil purification, LV/MV panels, containerised solutions, and much more, all from RMM.
“We have invested a lot of money into equipment for oil, and we put up a special test bed that we designed in-house. We have had very good reviews and a number of clients that have come through saying this is the best test bed that they have ever seen,” says Wagner.
Typically, the company works closely with international engineering consultancy firms to ensure world-class rollout. From South Africa, RMM is currently preparing 28 transformers for a project in Zimbabwe, as well as a R20 million order for the second phase of a mine extension project in Zambia, and the first eight of a big contract in Congo.
“There was a company that supplied 40 transformers to a mine and all 40 failed,” explains Wagner. “The cooling system was made up of big fans pulling air from the surface and allowing dust and dirt to blow onto the transformers. The mine engineers came to us to replace all of these transformers and we are busy with the first eight right now with the balance to come next year. We use a closed loop system with a patented heat exchanger and an external fan. Our unit has received a lot of design work and is best-in-class.”
UNDENIABLE QUALITY
With mining activity ramping up in 2023, and innovation and reinvention at the heart of many expansion projects, ensuring there is no slowdown in Edenvale is vital for RMM. The factory is home to a sophisticated solar energy back up system, and a wind turbine to produce green power for the site, both connected to an industrial battery system.
Working in confidence that even with severe loadshedding RMM will not be forced to slowdown, the team continues to build both internally and externally. Wagner encourages frequent upskilling activity and the result is an undeniable reputation for excellence.
“The design engineers are licensed with the engineering board and they take several courses. We pay for all of that and they are upskilled nicely. The private sector is proactive in making plans and that keeps people moving forward. We recently sent an electrician on a course to become an electrical engineer – we are upskilling, we are not waiting. We are building the skilled workforce of the future. SolidWorks runs its own private education system where you work online for certificates. We invested R500,000 in a programme called EPLAN to produce schematic drawings. This allows us to do 3D modelling and comprehensive plans.
“There are a lot of others out there, but when it comes to cast resin and SGB transformers, we have developed a special technology,” Wagner details.
“People tried cast resin transformers, a dry model cooled by air. They cracked because of expansion and contraction of the wire. SGB came up with a special system for the wiring using epoxy resin. We have sold more than 600 of these transformers and never had a crack – this is the reason people buy from us. Our quality is undeniable; made in Germany. We import the core transformer and wrap it locally. Our products are designed to last at least 20 years in a mine.”
Conditions in deep African mines are harsh. Hot, hard, and dry, and with unique characteristics that those elsewhere in the world. Operating at the extremes – that advance as mines go deeper – means that standard transformers are simply not good enough.
“We overspec our units,” states Wagner. “European manufacturers tend to only understand +20 degrees at 1000m above sea level. We work, as standard, at 50 degrees, 1800m above sea level. With us, there are no heating problems. Our reputation is built around that and that is why we are a sole supplier of cast resin transformers to some of the biggest mining companies in the world. There is a special housing which means you can hang the transformer upside down to send down the shaft before moving it across. It’s made out of heavy-duty steel and is very robust, weighing in at 4.5 tons.”
Considering RMM has one of the most reliable, most-recognised, and locally engineered products available, and that mining as we know it still requires electricity deep in the shaft, the company is buoyant about the future. Encouraged by the rampant demand for technology minerals across southern Africa, RMM is strongly positioned.
“We are in a niche market, supplying a top-class product to companies that are prepared to pay for it,” says Wagner.
“We don’t want to become one of the largest transformer manufacturers in the world. We want to put out a quality product on time, keeping our customers happy. Our reputation is superb – I had the call from Ethiopia because of a word-of-mouth recommendation – and we want to keep it that way.”
RMM Project Engineers make the toughest of mining that little easier, and with growing demand from around the continent, it looks likely that the factory in Edenvale will only get busier.